Our processes
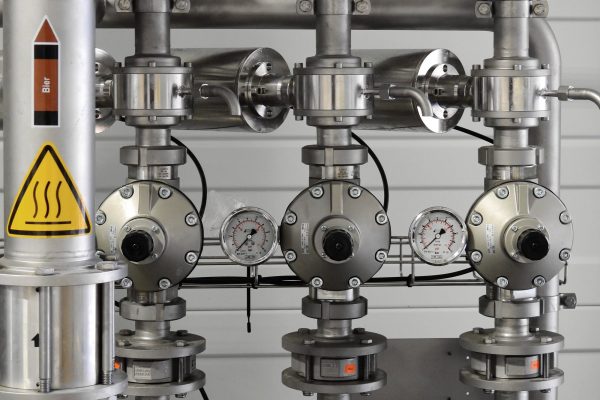
Passivation
As the corrosion resistance can differ between different types of stainless steel, so-called passivation of the material can be carried out. When stainless steel is mechanically grinded or polished, for example, the passive properties disappear and an active surface is obtained instead. This is a major disadvantage, especially in those environments where high corrosion requirements exist and an active surface on the part should be avoided. Passivation is an effective method that can be done after both pickling and electropolishing. Unlike that process, there is no dissolution of the metal during passivation, which means that accuracy requirements can be maintained. At Backmans Sliperi we carry out passivation using nitric acid which strengthens the protective oxide layer. After a generous rinse using deionised water, a high quality reinforced surface layer is achieved, free from iron particles and other substances that can cause possible corrosion.
Important! When passivating, it is very important that the parts are clean and free from various organic contaminants. Therefore, a very thorough rinsing and cleaning is carried out at the end of our pickling process.
Used in the process:
- Nitric acid
- Water
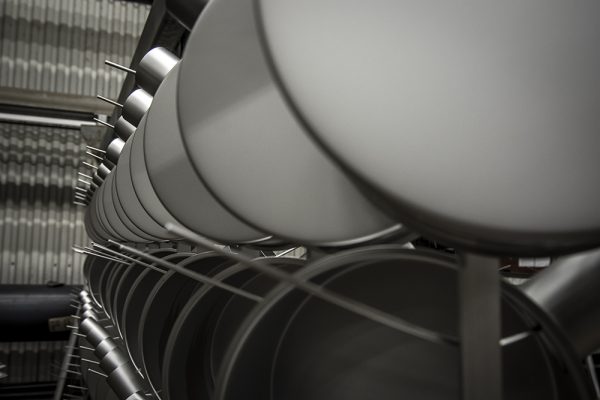
Pickling
Pickling is a process that first dissolves and removes any impurities on the surface of the material. The surface of the part is then given a protective passivation. Usually this is done on various types of heat-treated or welded stainless steel structures. In our equipment, so-called dip-bedding is carried out, which means that the entire part is lowered below the surface of the bath. This is a very effective process for removing everything from annealing scale, iron contaminants and welding oxides to residues from grinding wheels, abrasives, etc. The pickling process is completed with a generous rinse using deionised water, which restores the corrosion resistance of the material by restoring the chrome-depleted surface layer. To reinforce the surface layer after pickling, electropolishing is often a very good solution.
Important! Always make sure that the parts are clean from oil and grease.
Used in the process:
- Hydrofluoric acid
- Nitric acid
- Water
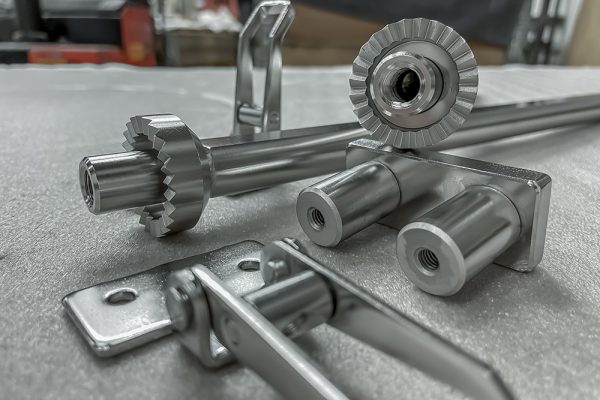
Electropolishing
Electropolishing removes a surface layer from the stainless steel. This provides a glossy finish, deburred edges and a smoothed surface. Most importantly, you get a metallic clean detail. The process itself is an electrochemical method which allows the crystal structure of the material to emerge in its purest form without any deformation. The process is completed with a generous rinse using deionised water. The major advantage of electropolishing is that it produces a polished surface with a low Ra-value, while maintaining the properties of the base material. The process is often used on parts for the food, nuclear and pharmaceutical industries where features are required to prevent contaminants or bacteria from sticking to surfaces. In short, electric polishing is an economical and rational method compared to mechanical polishing. In case of high demands on purity and passive protection, passivation is also recommended here.
Important! The best results are achieved when the parts are free of defects. Keep in mind that scratches, indentations and other damage will not be removed during polishing but will rather be enhanced.
Used in the process:
- Phosphoric acid
- Sulphuric acid
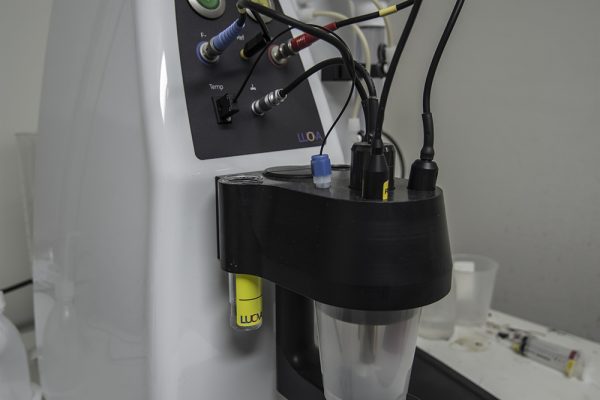
Laboratory
Our facility also includes a laboratory. It is a very important part of all our processes that the various baths in our production line are clean and free of impurities and similar. Therefore, regular sampling is carried out. In our laboratory we then analyse these samples from the various chemicals we use. This is all to ensure that the processes are carried out and that the facility delivers the highest quality, a very important task in order to achieve the high standards of accuracy that are required. Our laboratory consists of high-tech equipment that quickly helps us with our quality analyses. It is important for us that you as a customer can always rely on us as a supplier, and know that we never compromise on quality and accuracy.